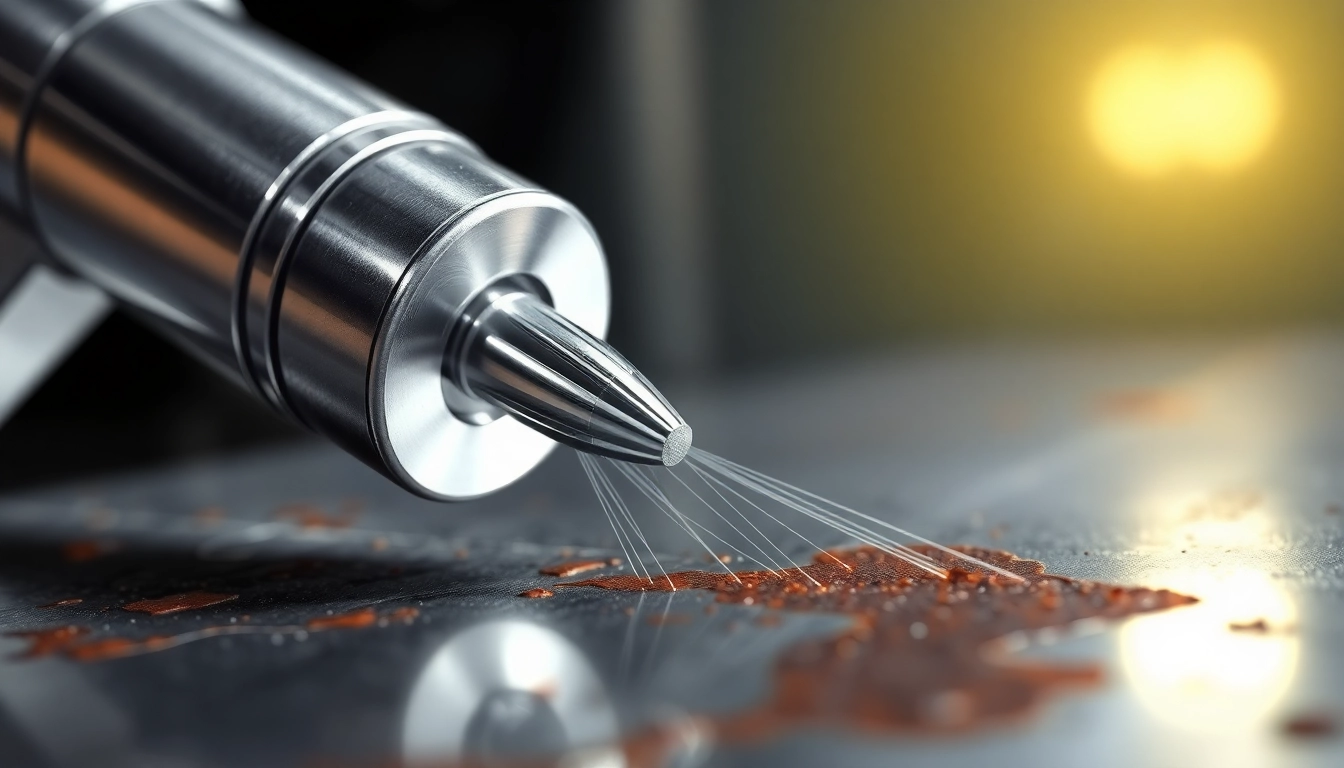
What is a Needle Gun?
Definition and Functionality
A needle gun, often referred to as a needle scaler, is a specialized pneumatic tool designed to remove rust, old paint, and undesired contaminants from metal surfaces. It utilizes a series of rapid, needle-like projections that strike the surface at high speeds, effectively dislodging unwanted materials without causing damage to the underlying metal. The functionality of the needle gun makes it indispensable in industries that require precision cleaning and surface preparation before subsequent treatments like painting or coating.
History and Evolution
The needle gun traces its origins back to the 19th century, primarily known as a firearm due to its needle-like firing mechanism, which struck a percussion cap. However, the modern interpretation of the needle gun has shifted towards its application as a scaling tool. Over the years, engineers have refined its design, leading to improvements in air pressure efficiency and usability. The needle scaler has evolved into electric and pneumatic models, providing versatility based on user preferences and the specific requirements of different jobs.
Types of Needle Guns Available
Needle guns can be categorized into two primary types based on their power sources: pneumatic and electric models. Pneumatic needle scalers are commonly used for heavy-duty applications due to their power and efficiency. They require a compressed air supply and are ideal for industrial environments. Conversely, electric needle scalers are often lighter, easier to handle, and suitable for smaller tasks, making them favorable for DIY projects and home use. Each type has distinct advantages depending on the nature of the job and the user’s needs.
How Needle Guns Work
Mechanics Behind Needle Guns
The effectiveness of a needle gun lies in its mechanism. The tool consists of multiple steel needles that move back and forth at high frequency, typically measured in beats per minute (BPM). This movement creates a scrubbing action that dislodges rust, paint, and other surface contaminants. The compressed air or electric motor drives the action, ensuring consistent performance. When using a needle scaler, it’s crucial to adjust the air pressure to suitable levels, often between 90 to 100 PSI for optimal efficiency.
Understanding Air Pressure and CFM Requirements
CFM, or cubic feet per minute, is a vital metric when operating a needle gun. Each model has specific air requirements that dictate performance. Typically, needle guns will range between 8-16 CFM at 90 PSI. Properly assessing your air compressor’s capabilities is essential to maximize efficiency and avoid operational hiccups. Understanding CFM requirements can significantly enhance the tool’s performance, ensuring that it operates effectively without straining the compressor.
Proper Usage Techniques
To achieve the best results while using a needle gun, adhere to the following techniques:
- Begin with a clean area to establish a base level of cleanliness.
- Maintain an appropriate angle while working to efficiently peel away layers of debris.
- Utilize consistent pressure yet avoid excessive force, which can damage the surface.
- Pay attention to the tool’s maintenance to ensure it continues operating efficiently.
By following these techniques, users can significantly extend the lifespan of their needle scalers while achieving optimal results.
Applications of Needle Guns
Surface Preparation for Painting
Before painting, achieving a clean surface free from contaminants is crucial. Needle guns are exceptional at preparing a surface by removing old paint, preventing new layers from peeling or flaking. By effectively preparing surfaces, needle guns ensure that the paint adheres properly, resulting in a smoother, more durable finish.
Rust and Contaminant Removal
One of the primary uses of needle scalers is removing rust from metal surfaces. Rust can not only diminish the aesthetic appeal of metal objects but also compromise the structural integrity. Using a needle gun allows for targeted rust removal while preserving the underlying metal. Beyond rust, needle guns also effectively eliminate mill scale and other unwanted materials, providing a thorough cleaning solution for metal surfaces.
Metal Fabrication and Repair
In the realm of metal fabrication and repair, needle guns facilitate a clean working environment. Whether for automotive applications, shipbuilding, or manufacturing, these tools are essential for ensuring that bonded surfaces are ready for welding or additional assembly. Their ability to reach into tight spaces and contours makes them ideal for various metalwork processes.
Choosing the Right Needle Gun
Key Features to Consider
When selecting a needle gun, consider the following features:
- Power Source: Evaluate whether a pneumatic or electric model fits your needs best.
- Weight and Ergonomics: Choose a lightweight model for prolonged use without fatigue.
- Needle Configuration: The number and configuration of needles can affect efficiency; more needles can mean faster cleaning.
- Adjustable Pressure Settings: Flexibility in settings allows for tailored usage across different materials.
Comparison of Electric vs. Pneumatic Models
Both electric and pneumatic needle guns come with unique advantages: electric needle guns are typically more portable and easier to use for smaller tasks, while pneumatic models provide better power for industrial applications. Electric tools can offer convenience but may lack the intensity of pneumatic versions, which can handle more demanding jobs. Assessing the intended use will help determine the best option for specific applications.
Top Brands and Models to Consider
The market is filled with reputable brands that produce high-quality needle guns, including Ingersoll Rand, Chicago Pneumatic, and Von Arx. Each brand offers various models catering to different needs. For those interested in the Von Arx needle gun, the needle gun boasts exceptional features suited for intense surface preparation tasks. When selecting a model, consider user reviews, warranty, and availability of replacement parts.
Maintenance and Safety Tips
Regular Maintenance Practices
Regular maintenance is crucial for ensuring the longevity and performance of needle guns:
- Inspect needles for wear and replace as necessary to maintain effectiveness.
- Clean the air inlet filter regularly to prevent air supply issues.
- Lubricate moving parts according to the manufacturer’s guidelines to reduce friction.
- Store the tool in a dry, safe place to protect it from damage and corrosion.
Implementing these practices will help sustain optimal performance and prolong the life of the tool.
Safety Gear and Precautions
When using a needle gun, safety should always be a priority. Essential safety gear includes:
- Safety goggles to protect eyes from flying debris.
- Hearing protection, as the noise generated can be significant.
- Respirators to prevent inhalation of dust or particles that may be released during use.
- Work gloves to shield hands from sharp edges and vibrations.
By wearing appropriate gear, users can mitigate risks associated with operating needle guns.
Common Troubleshooting Issues
Despite their robust design, users may encounter issues with needle guns:
- Inconsistent Performance: This can be due to inadequate air pressure or dirty air filters, so ensure regular maintenance checks.
- Needles Breaking: This may happen if too much pressure is applied; adjust usage techniques accordingly.
- Pneumatic Tools Not Operating: Check for compressor issues or leaks in air lines.
Identifying and addressing these common issues can save time and repair costs, ensuring the tool operates efficiently.