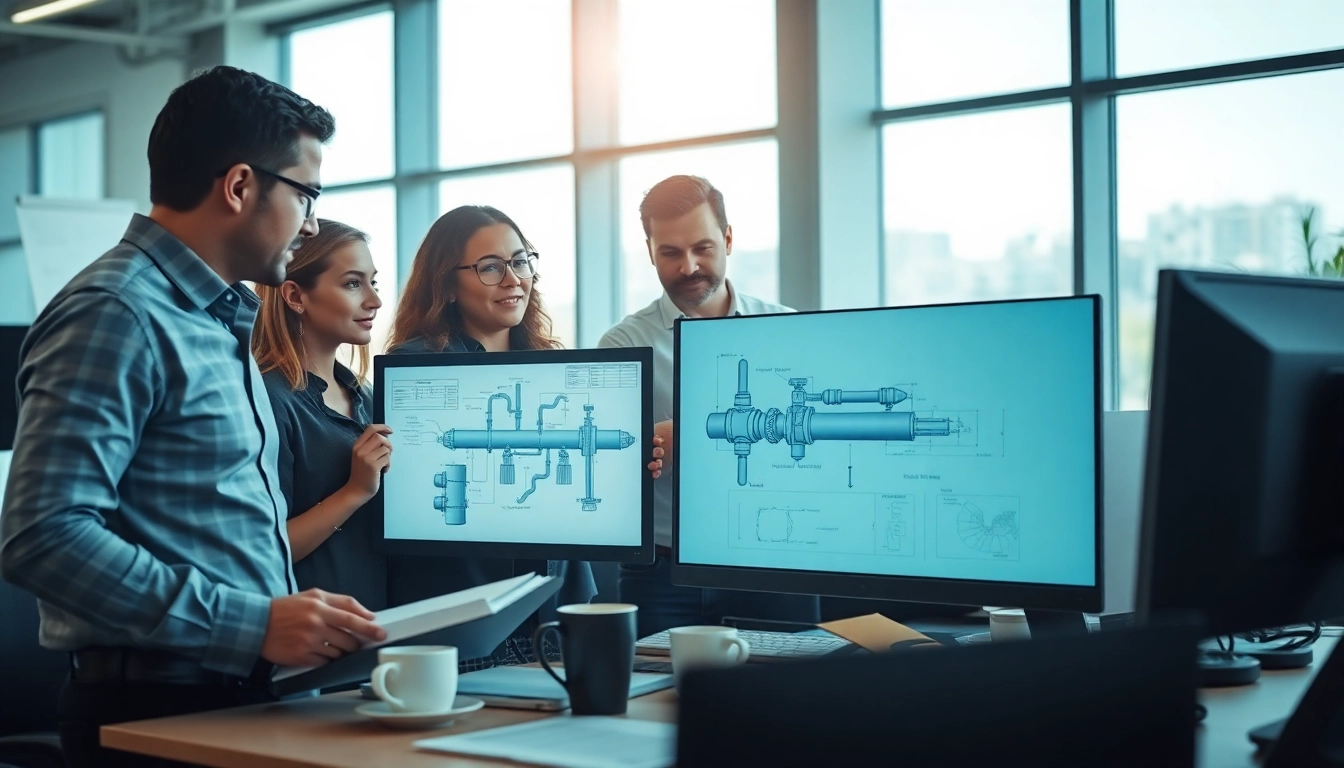
Understanding Pipe Stress: Core Concepts
When it comes to engineering, particularly in the realms of chemical processing, oil refineries, and power generation, understanding pipe stress is crucial. The structural integrity of piping systems under various loading conditions determines the safety and performance of operations. In this article, we dive deep into the fundamentals of pipe stress analysis, the significance of this discipline in engineering sectors, the common challenges companies encounter, and advanced methods that leading pipe stress Company employ to optimize systems.
The Fundamentals of Pipe Stress Analysis
Pipe stress analysis involves evaluating the forces and moments that coupling pipes can experience throughout their lifespan. This includes evaluating thermal expansion, weight loading, and dynamic forces that arise during operation. Key concepts include:
- Thermal Expansion: When temperature increases, pipes expand. Without considering this factor, structures may experience undue stress leading to failure.
- Weight Consideration: The weight of the piping itself, along with the contents it transports, can significantly impact its structural integrity.
- Supports and Restraints: Properly placing supports helps manage expansion and contraction, reducing stress on piping systems.
Importance of Pipe Stress in Engineering
In engineering, effective pipe stress management plays a vital role in enhancing safety, reducing downtime, and prolonging the life of the piping systems. Here are several reasons why pipe stress analysis is important:
- Ensures Safety: Assessing stress points can prevent catastrophic failures, safeguarding both personnel and assets.
- Reduces Maintenance Costs: By identifying potential stress-related issues early, companies can avoid costly repairs and unplanned outages.
- Enhances Efficiency: Optimized piping systems lead to smoother operations, which improves overall system efficiency.
Common Pipe Stress Challenges Faced by Companies
While the importance of pipe stress analysis is clear, numerous challenges complicate its application. Here are some of the most common:
- Complex Geometries: Irregular structures and systems make calculations cumbersome, often leading to analytical errors.
- Lack of Data: Incomplete material data can hinder accurate stress assessments.
- Dynamic Loading Conditions: Changes in operational parameters can introduce unpredictable stress variables that need continual monitoring.
Advanced Techniques in Pipe Stress Analysis
Tools and Software Used by Leading Pipe Stress Companies
Advancements in technology have led to the development of sophisticated software for pipe stress analysis, which streamlines processes and increases accuracy. Some widely recognized tools include:
- AutoPIPE: Renowned for its user-friendly interface, AutoPIPE aids in calculating pipe stress under various loading conditions.
- CAESAR II: A powerful tool for comprehensive pipe stress analysis, leverages finite element analysis principles to provide robust solutions.
- ANSYS: This tool offers simulation capabilities to study the impact of fluid dynamics on piping systems.
Integrating Finite Element Analysis in Pipe Stress
Finite Element Analysis (FEA) has revolutionized pipe stress assessments by enabling engineers to visualize stress distribution across complex geometries. FEA works by dividing structures into smaller, manageable elements, reducing the time required to evaluate performance under loaded conditions. Benefits of integrating FEA include:
- Increased Accuracy: High-fidelity models allow for precise predictions of stress and strain across various sections of piping systems.
- Improved Design Features: Engineers can test different configurations quickly, resulting in optimized designs that take stress into account.
- Enhanced Risk Management: Understanding stress points helps identify potential failure modes before they occur, allowing for proactive measures.
Case Studies: Successful Applications of Advanced Techniques
The practical application of advanced pipe stress analysis techniques not only exemplifies their relevance but also provides critical insights into problem-solving strategies in real-world situations. Consider the following examples:
- Petrochemical Industry: A leading petrochemical manufacturer employed sophisticated software to analyze a new pipeline system. By applying advanced simulation techniques, the company was able to reduce potential thermal expansion forces by 30%, leading to significant cost savings in both materials and labor.
- Power Plant Upgrade: During a recent upgrade to a power plant, engineers used FEA to optimize the design of the piping system to reduce vibrations, which historically led to premature failures.
- Water Treatment Facilities: An analysis of a critical pipeline in a treatment facility addressed issues of internal pressure under dynamic loading, successfully facilitating the design of a more durable system.
Best Practices for Effective Pipe Stress Management
Regular Maintenance and Inspections
Regular maintenance and inspections are essential in identifying stresses that could lead to failures. Best practices include:
- Scheduled Inspections: Conducting regular inspections based on operational standards helps identify possible wear and tear early.
- Analytics and Reporting: Documenting stress analysis results structures historical data and highlights trends that inform future decisions.
- Predictive Maintenance: Employing data analytics to predict potential failures can significantly decrease downtimes.
Design Considerations for Pipe Stress Reduction
Engineers must make informed design choices that take future stress into account right from the initial stages. Effective strategies include:
- Material Selection: Choosing materials that can better withstand thermal and pressure changes can extend the lifespan of the piping.
- Support Placement: Properly designed supports can mitigate stress; analyzing support placement during the design phase is crucial.
- Expansion Loops and Joints: Incorporating expansion joints or loops can significantly reduce stress from thermal expansion.
Collaboration Between Engineers and Design Teams
For effective pipe stress management, collaboration among multidisciplinary teams is essential. Builders and engineers must work closely during the design phase to discuss potential stress points, ensuring that all design considerations are aligned with operational constraints. Establishing regular communication channels and fostering a culture of collaboration will lead to more resilient and optimized designs.
Measuring Performance in Pipe Stress Analysis
Key Metrics for Evaluating Pipe Stress Outcomes
Evaluating the effectiveness of pipe stress analysis requires specific performance metrics. Important indicators include:
- Failure Rates: Tracking the historical failure rates of piping systems provides insight into stress management effectiveness.
- Cost Savings: Monitoring costs related to maintenance and repairs can show economic benefits derived from proactive stress management.
- Operational Efficiency: Assessing production output relative to downtime can reveal the impact of effective pipe stress management on overall efficiency.
Continuous Improvement Strategies
The field of pipe stress analysis is continually evolving. Implementing a continuous improvement strategy is vital for staying ahead of challenges. Steps include:
- Data-Driven Decisions: Leveraging big data analytics can provide insights into performance trends, enabling timely interventions.
- Feedback Loops: Establishing feedback protocols from maintenance teams can improve the design of future piping systems.
- Training and Development: Regular training for engineering personnel on updated techniques and technologies fosters a culture of ongoing improvement.
Real-world Examples of Performance Improvement
Companies adopting measures to improve pipe stress performance have noted significant advantages:
- Chemical Plant: A chemical manufacturing plant implemented a robust insulative coating on its piping system, which reduced thermal expansion stress and improved operational efficiency by 15%.
- Oil Refinery: An oil refinery utilized predictive maintenance techniques, which led to a 40% decrease in unexpected downtimes associated with piping failures over a two-year period.
The Future of Pipe Stress Analysis
Emerging Trends in Pipe Stress Engineering
The landscape of pipe stress analysis is ever-changing. Emerging trends suggest greater emphasis on:
- Integration of AI: Artificial intelligence is becoming an integral aspect of stress analysis, allowing for predictive insights that were previously unattainable.
- Sustainable Materials: A focus on sustainable materials is expected to influence design choices, making them more resilient to stress factors.
- Automation and Remote Monitoring: Increased automation in monitoring stress levels leads to real-time responses to potential failures.
Impact of Digital Technologies on Pipe Stress Management
Digital technologies have significantly transformed how stress analysis is conducted. The integration of smart sensors and IoT devices allows for continuous monitoring of stress in real time, fostering immediate responses to any arising issues. As these technologies evolve, they offer the following advantages:
- Enhanced Data Collection: Sensors provide accurate data that can be quickly analyzed to mitigate risks related to stress.
- Greater Predictability: Advanced algorithms can analyze collected data effectively, leading to more accurate forecasts regarding stress points.
- Holistic Views: Digital dashboards can provide engineers with comprehensive insights into all aspects of piping systems.
Preparing for Future Challenges in Pipe Stress Analysis
Though advancements bring about exciting opportunities, challenges will persist, requiring companies to prepare adequately. Strategies to consider include:
- Continuous Learning: Adaptation to new trends and technologies through regular training will ensure engineering teams are well-equipped.
- Early Adoption: Companies willing to invest in new technologies before they become mainstream can gain a competitive advantage.
- Collaboration Among Industries: Engaging in partnerships can foster innovation and improve overall stress management approaches.