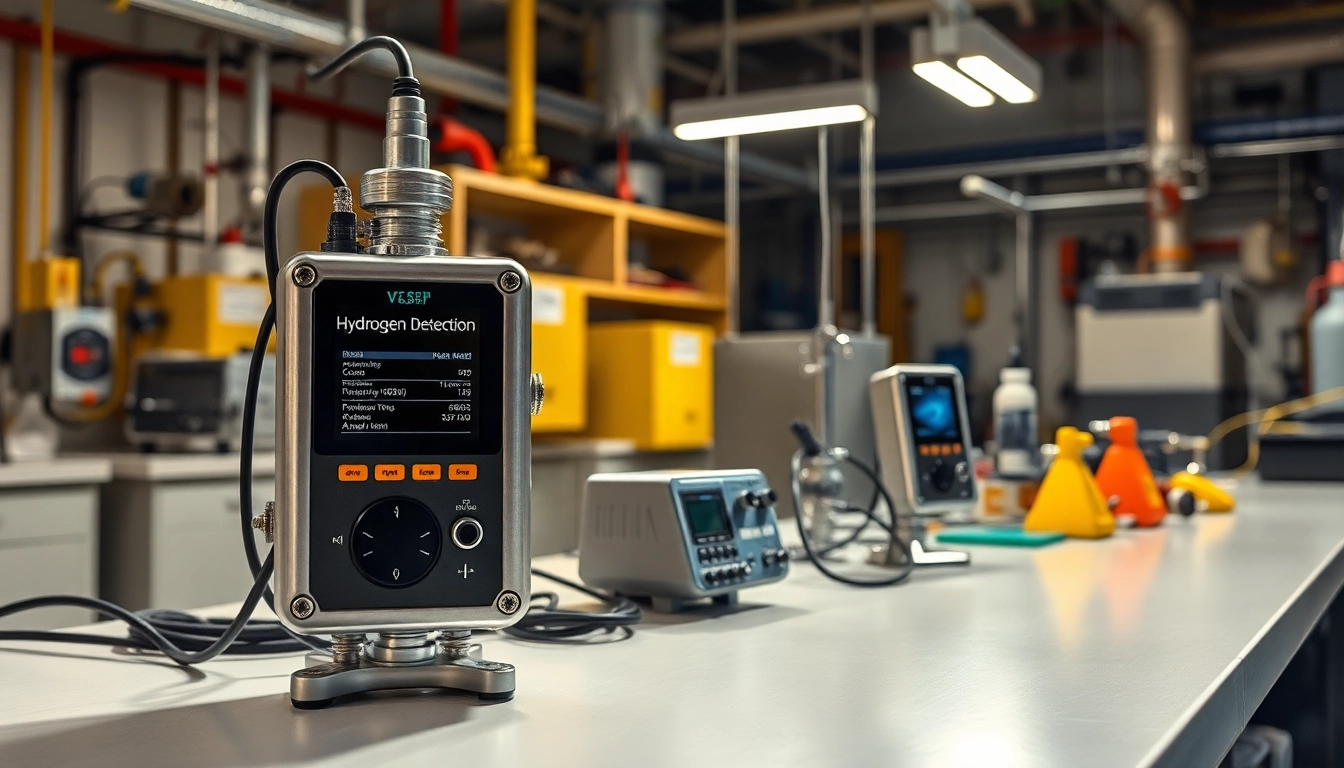
Understanding Hydrogen Detection
What is Hydrogen Detection?
Hydrogen detection refers to the methods and technologies employed to identify the presence and concentration of hydrogen gas in various environments. It is crucial for ensuring safety in settings where hydrogen is produced, used, or stored, as hydrogen is highly flammable and can pose significant hazards. Hydrogen detection systems employ various sensor technologies to monitor the gas concentrations and provide alerts when levels exceed safe thresholds.
Hydrogen detection is vital in industries such as chemical manufacturing, oil and gas refining, and emerging technologies like hydrogen fuel cells. Effective monitoring can prevent hazardous situations and contribute to compliance with safety regulations. For more information on hydrogen detection technologies and products, visit Hydrogen detection.
The Importance of Hydrogen Monitoring
The monitoring of hydrogen is imperative due to its unique properties. Hydrogen is the lightest and most abundant element in the universe, but it can form explosive mixtures with air and is highly flammable, igniting easily in the presence of a spark. Thus, monitoring is critical in areas where hydrogen may leak, such as storage spaces, industrial facilities, and during transportation.
Inadequate detection systems can lead to significant risks, including fire, explosions, and injuries to personnel. Effective hydrogen monitoring helps mitigate these risks by ensuring that safety protocols are followed, allowing for timely responses to gas leaks. Additionally, as industries pivot towards greener methods and hydrogen-powered technologies, the role of hydrogen detection will only become more pronounced, reinforcing the need for robust monitoring systems.
Common Applications of Hydrogen Detection
Hydrogen detection technologies find applications across various sectors, including:
- Chemical Manufacturing: Used to monitor hydrogen production processes and storage, ensuring worker safety and compliance with safety regulations.
- Oil and Gas Industry: Hydrogen is generated during refining and various chemical processes; thus, monitoring is essential to prevent explosions and fires.
- Automotive Sector: Fuel cell vehicles are emerging as a clean energy solution, requiring precise hydrogen monitoring systems to ensure safety.
- Energy Sector: Hydrogen storage facilities, particularly in renewable energy setups, use detection systems to ensure safe operations.
Types of Hydrogen Detectors
Electrochemical Sensors for Hydrogen Detection
Electrochemical sensors are one of the most commonly used technologies for hydrogen detection. These sensors work by employing an electrochemical reaction that generates a current proportionate to the concentration of hydrogen in the environment. The benefits of electrochemical sensors include high sensitivity and selectivity to hydrogen, making them ideal for a wide range of applications.
These sensors are often used in personal safety equipment, industrial monitoring systems, and portable devices due to their compact nature and low power requirements. Calibration is essential for maintaining accuracy, and regular maintenance can extend the life of these sensors significantly.
Catalytic and Metal Oxide Sensors
Catalytic sensors detect hydrogen by using a heat generation principle. When hydrogen comes into contact with the catalyst, it oxidizes, leading to a temperature increase that is measured to determine the presence of gas. These sensors are robust, but they can be affected by the presence of other gases and are typically used in fixed installations.
Metal oxide sensors, on the other hand, utilize semiconductor materials to detect gas concentrations. When hydrogen molecules come in contact with the metal oxide surface, they change the electrical resistance of the sensor, indicating the hydrogen levels. While these sensors are sensitive and can detect low concentrations of hydrogen, they may require temperature control to optimize their performance.
Comparing Portable vs Fixed Hydrogen Detectors
When selecting a hydrogen detection system, users must decide between portable and fixed detectors. Portable detectors are ideal for workers who need flexibility in their monitoring tasks, providing immediate feedback on hydrogen levels in various environments. They are especially useful in transient applications, such as during maintenance or inspections.
Fixed detectors, however, are strategically installed around facilities, providing continuous monitoring of potential hydrogen leak sites. These systems typically integrate into alarm systems, alerting personnel to critical levels of gas immediately. Each type has its merits, and often, a combination of both offers the best safety coverage.
How Does Hydrogen Detection Work?
Operating Principles of Hydrogen Sensors
Hydrogen sensors operate on various principles depending on the technology being used. The majority of gas detection technologies, including electrochemical and catalytic sensors, rely on the interaction between hydrogen gas and specific materials that produce measurable changes in physical properties, such as electrical current or resistance.
For example, electrochemical sensors create a chemical reaction between hydrogen and the sensor’s active material. This reaction generates a current that reflects the gas concentration. Similarly, catalytic sensors measure temperature variations due to the combustion of hydrogen. Understanding these operational principles is key to selecting the appropriate sensors for specific applications.
Choosing the Right Detection Method
Choosing the right hydrogen detection method involves considering factors such as the environment, potential hazards, required response time, and budget. It is essential to perform a risk assessment to identify areas where hydrogen may accumulate and the likelihood of a leak occurring.
For environments with fluctuating temperatures and high humidity, sensors with robust calibration and maintenance plans are necessary. Conversely, in controlled environments, simpler detector types may suffice for risk mitigation. Consulting with experts in gas detection is often helpful when making this decision, ensuring that safety measures are appropriate.
Calibration and Maintenance of Sensors
Effective calibration and maintenance are critical elements of any hydrogen detection system. Regular calibration ensures that sensors maintain accuracy over time, recalibrating them according to manufacturer specifications after certain exposure levels or periods of usage is essential.
Routine maintenance includes cleaning sensors, checking for obstructions, and reviewing the sensor responses under controlled conditions. Implementing a maintenance schedule is best practice to extend the lifespan of detectors, ensuring that they function correctly when needed.
Implementing Hydrogen Detection Solutions
Best Practices for Safety in Hydrogen Environments
Implementing best practices for safety in hydrogen environments is fundamental to effective risk management. First, proper risk assessments should be conducted to evaluate potential leak sources. Employee training is vital in promoting safe work habits and understanding the operation of detection devices. Moreover, integrating gas detection alarms into the workplace can enhance awareness and readiness to respond to leaks.
It is also crucial to ensure proper ventilation in areas where hydrogen is used or stored, which mitigates the risk of gas accumulation. Regular drills and procedures for emergency response should be established to prepare the workforce for any hydrogen-related incidents.
Regulatory Standards for Hydrogen Detection
Regulatory standards significantly influence the implementation of hydrogen detection technologies. Organizations such as the Occupational Safety and Health Administration (OSHA) and the National Fire Protection Association (NFPA) provide guidelines to ensure safe hydrogen handling and detection. Compliance with these regulations is essential for maintaining workplace safety and avoiding legal ramifications.
It is essential to stay informed on local, national, and global safety regulations as they can affect detection system requirements. Regular reviews and audits can help organizations maintain compliance and enhance their safety protocols.
Integrating Detection Systems in Industry
Integrating hydrogen detection systems within existing industrial processes requires careful planning. It involves not only selecting the appropriate technology but also ensuring that systems can communicate with other safety systems, such as alarms and ventilation controls.
Collaborating with safety engineers and gas detection professionals helps streamline the integration process, allowing for customized solutions tailored to specific industrial environments. This cooperation is crucial to address the unique challenges and requirements each facility may encounter.
Future Trends in Hydrogen Detection Technologies
Emerging Technologies for Enhanced Monitoring
As concerns about safety become more pressing with the increasing utilization of hydrogen, numerous emerging technologies in hydrogen detection are being developed. Innovations like nanomaterials and advanced semiconductor technologies are being explored to enhance sensitivity and lower detection thresholds. These technologies could lead to more reliable and faster detection capabilities.
Moreover, portable hydrogen detectors are becoming more sophisticated, incorporating advanced features such as data logging and real-time analytics. These features improve operational efficiencies and safety across various industries.
The Role of IoT in Hydrogen Safety
The Internet of Things (IoT) is increasingly being applied to hydrogen detection technologies. IoT-enabled sensors allow for remote monitoring and data analytics, providing valuable insights into hydrogen levels in real time. These systems can alert personnel to hazardous conditions instantly, streamlining response efforts.
Furthermore, IoT integration supports predictive maintenance, wherein data collected from sensors helps anticipate sensor failures, reducing downtime and ensuring reliable safety measures.
Predictive Maintenance and Data Analytics
Incorporating data analytics into hydrogen detection systems enables organizations to move beyond reactive safety measures. By utilizing historical data collected from sensors, companies can predict potential issues before they escalate into safety hazards. This approach enhances the longevity of detection systems and optimizes maintenance schedules based on actual usage patterns.
Predictive maintenance nurtures a proactive safety culture that aligns with advanced industrial practices, leveraging information for continuous improvement in workplace safety monitoring.