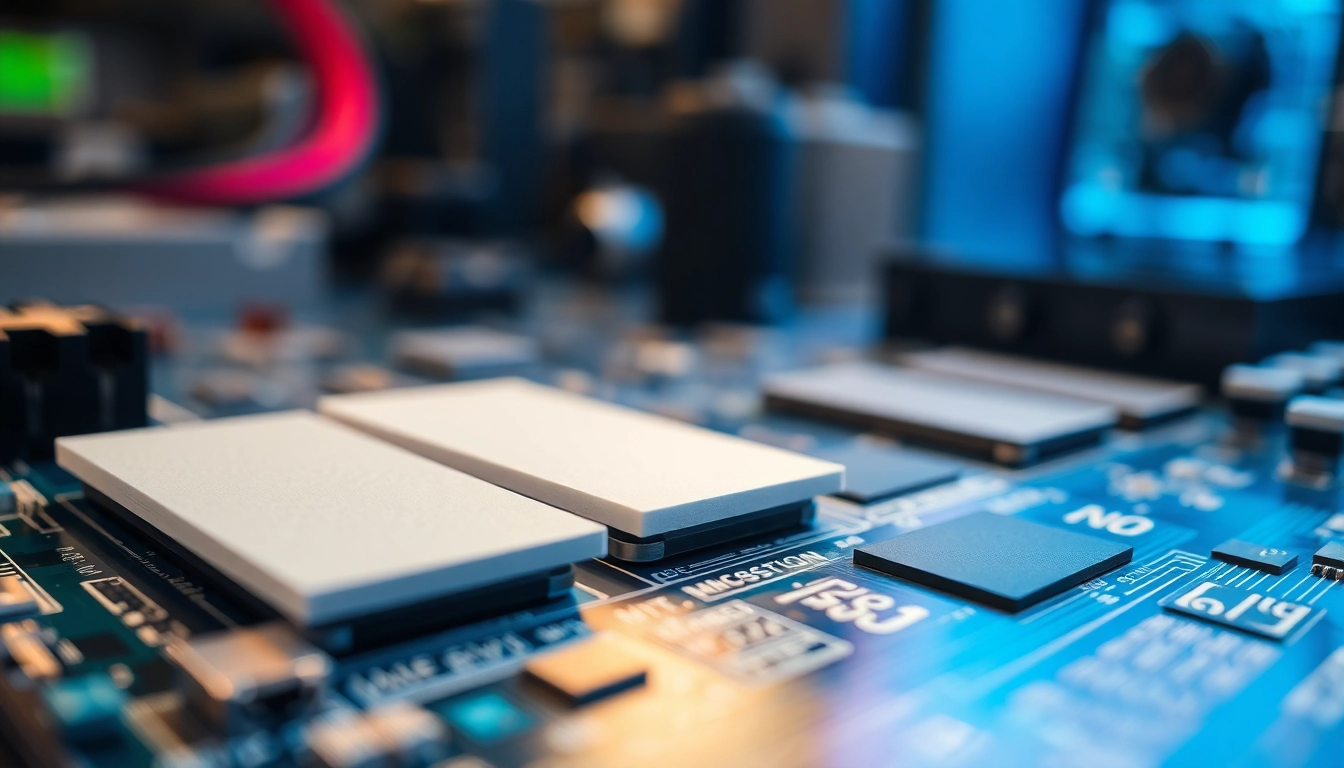
Understanding Thermal Management Materials
In today’s technology-driven world, thermal management materials are of paramount importance, particularly within the realms of electronics and automotive industries. As devices become smaller and more powerful, the need for effective heat dissipation solutions grows, thereby making thermal management materials essential for maintaining optimal performance and reliability of electronic systems.
What Are Thermal Management Materials?
Thermal management materials refer to a diverse range of products engineered to dissipate heat effectively and ensure proper thermal regulation within various applications. These materials facilitate heat transfer across components, helping to prevent overheating, enhance operational efficiency, and extend the lifespan of electronic devices.
Key Types and Their Functions
Thermal management materials can be broadly classified into several categories based on their specific functions and applications. Each type addresses unique thermal challenges within an electronic ecosystem:
- Thermal Interface Materials (TIMs): These materials are utilized to enhance the thermal contact between heat sources (like microprocessors) and heat sinks, reducing thermal resistance and allowing for efficient heat transfer.
- Thermal Gap Pads: Used to fill spaces between components, these pads provide excellent thermal conductivity while being compressible and compliant, allowing them to conform to surface irregularities.
- Thermal Greases and Gels: These viscous materials are designed to improve the thermal conductivity between surfaces by filling microscopic gaps and enhancing heat flow.
Importance in Electronics
In electronic applications, heat generation is inevitable. The efficiency of thermal management materials is crucial, as they help maintain the optimal operating temperature, thus safeguarding sensitive components from heat-related stress and damage. Effective thermal management not only safeguards performance but also contributes to energy efficiency, making them indispensable in modern electronic design.
Types of Thermal Management Materials
Thermal Interface Materials (TIMs)
Thermal Interface Materials play a critical role in enhancing heat dissipation in electronic assemblies. These materials are designed to fill the microscopic voids between mating surfaces, significantly improving heat transfer capabilities.
TIMs can be found in various forms, including:
- Thermal Greases: Typically silicone-based, these pastes provide excellent thermal conductivity but require careful application to avoid excess thickness that could decrease performance.
- Thermal Adhesives: These serve a dual purpose of bonding components while also conducting heat. They are particularly useful in applications where mechanical stability is a concern.
Thermal Gap Pads
Thermal gap pads are elastomeric materials that provide reliable thermal conductivity while maintaining compressibility. They are ideal for applications where there are gaps between components that need to be filled to enhance thermal transfer. These pads come in various thicknesses and thermal conductivities, making them suitable for a wide range of applications.
Common uses of thermal gap pads include:
- Between heat sinks and electronic components
- In power semiconductor packages
- As a thermal interface in battery management systems
Thermal Greases and Gels
Like TIMs, thermal greases and gels are designed to improve the thermal interface between components. They typically consist of a silicone base mixed with thermally conductive fillers. Unlike solid pads, they can provide better conformability and can be advantageous in applications where components may have uneven surfaces or variations in geometry.
However, the performance of greases and gels can be affected by environmental factors such as temperature and pressure, as well as the potential for pump-out or degradation over time.
Applications of Thermal Management Materials
Electronics Cooling Solutions
A significant portion of thermal management materials is devoted to electronics cooling, particularly in high-performance computing, telecommunications, and consumer electronics. The effective management of heat in these applications is crucial to ensure reliability and enhance performance.
Some specific cooling solutions include:
- Heat Sinks: Utilizing TIMs and thermal pads to enhance the efficiency of heat sinks in processors.
- Liquid Cooling Systems: Employing thermal conductive compounds in the interface between pipes and cooling blocks.
LED Lighting Applications
The rapid growth of LED technology has led to a need for efficient thermal management solutions in lighting applications. LEDs generate significant heat, which can affect their life span and performance if not managed correctly. Thermal management materials help maintain optimal temperatures, thus ensuring longevity and effectiveness of LED lights.
Automotive Heat Management
In automotive applications, thermal management materials are instrumental in managing heat from engines, batteries in electric vehicles, and even electronic control units. Effective thermal management ensures that components operate within specified temperature limits, contributing to safety and performance.
Examples include:
- Use of thermal adhesives and insulators in power electronics.
- The integration of thermal pads in battery systems to enhance heat dissipation.
Selection Criteria for Thermal Management Materials
Thermal Conductivity and Resistance
When selecting thermal management materials, the primary consideration is thermal conductivity, which indicates how effectively a material can transfer heat. The effectiveness is also influenced by thermal resistance, which should be minimized to ensure efficient heat flow between components.
Materials are typically compared based on their thermal conductivity ratings, specified in Watts per meter-kelvin (W/mK). Higher values indicate better heat transfer capabilities, making them preferable for applications that generate significant amounts of heat.
Material Compatibility
It is crucial to ensure that the selected thermal management material is compatible with both the electronic components it will interface with and the environmental conditions it will endure. Factors include:
- Chemical Resistance: Ability to withstand exposure to various chemicals or adhesives that might be present in applications.
- Temperature Tolerance: Ensuring both mechanical and thermal properties remain stable across anticipated operational temperatures.
Environmental Considerations
With increasing awareness regarding sustainability, the environmental impact of thermal management materials is becoming increasingly important. Manufacturers and designers are seeking materials that not only perform well thermally but are also eco-friendly. The use of recyclable materials, as well as compliance with environmental regulations, is becoming a standard in selection criteria.
Future Trends in Thermal Management Technologies
Advancements in Material Science
The field of thermal management materials is rapidly evolving, with advancements in material science leading to innovative products. Emerging materials, including phase change materials (PCMs) and nanomaterials, are paving the way for higher performance and efficiencies in heat transfer, addressing both current challenges and future demands.
For example, developments in the use of graphene, known for its superior thermal conductivity, show promise for next-generation TIMs and other thermal management solutions.
Smart Thermal Management Solutions
As technology continues to advance, the integration of smart materials that respond to varying thermal conditions is on the rise. Smart materials can adapt their properties based on temperature fluctuations, thus providing dynamic thermal management. This adaptability can enhance performance, especially in environments with rapidly changing thermal profiles.
Sustainability in Thermal Management
Finally, the push for sustainability will significantly influence the future of thermal management materials. As industries globally adopt greener practices, thermal management solutions that utilize sustainable materials and manufacturing processes will become increasingly prevalent. Emphasizing energy efficiency, recyclability, and reduced environmental impact will guide the development of next-generation thermal management solutions.