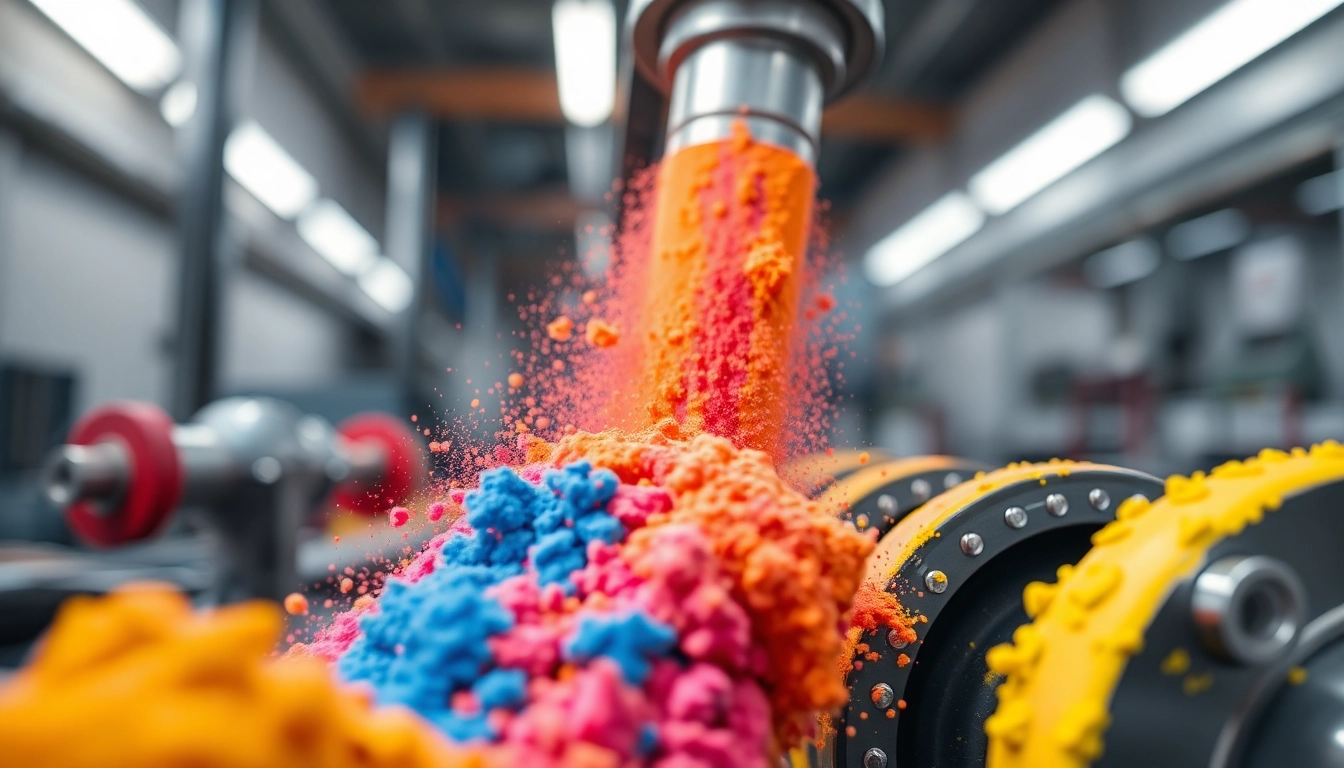
Understanding Powder Coating Basics
Powder coating is a sophisticated finishing process that has significantly shaped the industrial landscape. Defined as a dry finishing process, it consists of applying a free-flowing, dry powder to various metal surfaces. Unlike conventional liquid paint, which relies on solvents to dissipate, powder coating utilizes a technology that fuses the coating material to the substrate when cured at high temperatures. This method results in a hard finish that is more durable and protective than traditional painting methods, catering to industries ranging from automotive to consumer goods.
What is Powder Coating?
At its core, powder coating involves the electrostatic application of finely ground particles of pigment and resin, which are then cured under heat to form a solid coating. The process begins with the substrate, often metal, being cleaned and prepped to ensure optimal adhesion. The charged powder sticks to the grounded surface due to the electrostatic attraction. Once evenly distributed, the coated item is subjected to heat, typically in a curing oven, where the powder melts and flows into a smooth layer, bonding with the surface to create a tough, protection layer.
Benefits of Powder Coating Over Traditional Paint
Powder coating presents numerous advantages compared to traditional liquid paint, including:
- Durability: Powder-coated surfaces typically exhibit enhanced resistance to scratches, chipping, fading, and wear. The chemical bonds formed during curing result in a thicker coating, making it harder and more resistant than conventional paint.
- Environmental Benefits: Powder coating is environmentally friendly since it does not contain volatile organic compounds (VOCs). This means that it releases fewer harmful emissions into the atmosphere during application.
- Cost-Effectiveness: While the initial investment in powder coating equipment can be higher than that for liquid paints, the longevity and durability of the finish mean fewer repaints over time, leading to cost savings.
- Variety of Finishes: Powder coating offers a wide array of textures, finishes, and colors, opening up creative possibilities that traditional painting often can’t match.
- Efficiency: The application process is generally faster, and excess powder can be reclaimed and reused, minimizing waste.
Common Applications and Industries Using Powder Coating
Powder coating is utilized across various industries due to its versatility and robust nature.
- Automotive: From frames to exterior parts, powder coating provides automotive components with a durable and aesthetically pleasing finish that can withstand harsh conditions.
- Architecture: Architectural elements, including window frames, railings, and outdoor furniture, benefit from powder coating’s protective qualities, enhancing both durability and aesthetics.
- Consumer Goods: Items such as appliances, furniture, and electronics use powder coating for finishes that are both durable and visually appealing.
- Industrial Equipment: Machinery parts often require finishes capable of withstanding abrasions and harsh environments, making powder coating a practical choice.
The Powder Coating Process Explained
Understanding the powder coating process is essential for anyone looking to apply this technique, either personally or professionally. Each step plays a vital role in achieving a high-quality finish.
Preparation of Surfaces for Powder Coating
The preparation phase is crucial for ensuring that the powder bonds well with the surface. This process includes:
- Cleaning: Surfaces must be thoroughly cleaned to remove dirt, grease, oils, and old paint. Common methods include blasting, ultrasonic cleaning, or chemical cleaning.
- Etching: Some substrates may require etching or sanding to create a surface texture that aids in adhesion.
- Pre-Treatment: Applying a pre-treatment layer, like phosphate coating, can enhance adhesion and corrosion resistance.
Choosing the Right Powder Coating Material
Selecting the appropriate powder is critical to achieve the desired finish and performance. There are two main types of powders:
- Thermosets: These powders cure and create a hardened film through a chemical reaction when heated, making them suitable for various applications.
- Thermoplastics: These powders can be reheated and remolded without significant chemical change, allowing for repairs and reworking.
Additionally, powder coatings can be categorized further by their finish, such as Polyester, Epoxy, Hybrid, and more, each with different properties and applications.
Steps in the Powder Coating Application
The application of powder coating follows several streamlined steps:
- Electrostatic Application: The powder is sprayed onto the prepared surface using an electrostatic gun that charges the powder particles, causing them to adhere to the item.
- Curing: The coated items are placed in an oven, where they are heated to a specific temperature to cure the powder. The curing time and temperature vary depending on the type of powder being used.
- Quality Control: After cooling, products undergo quality checks to ensure that the coating is uniform and meets specified standards.
Cost Analysis of Powder Coating Services
Deciding to invest in powder coating services can be influenced by various factors. Here, we break down the costs associated with this service.
Average Costs of Powder Coating
The costs associated with powder coating can vary significantly based on several factors including the size of the item, the complexity of the work, and the location of service. On average, the cost typically ranges from $50 to $430 per item, with many consumers reporting costs around $170. This pricing may include prepping, coating, and curing phases, but additional expenses may be incurred for custom colors or intricate designs.
Factors Influencing Powder Coating Prices
Several key factors influence the overall pricing for powder coating services:
- Size and Shape of the Object: Larger or more complex items may incur higher costs due to longer application and curing times.
- Type of Powder Used: Different powders carry varying costs; specialty powders may increase the total investment.
- Surface Preparation Requirements: The extent of cleaning and preparation required can impact costs due to additional labor and materials.
- Location: Regional pricing differences can affect costs; urban areas may see higher rates compared to rural counterparts.
DIY vs Professional Powder Coating Costs
DIY powder coating can be tempting for those looking to save on costs. However, a thorough cost analysis is essential. While initial materials and equipment may seem cost-effective, professional services often provide higher quality finishes due to specialized equipment and expertise. DIY also presents challenges such as inconsistent application, curing issues, and safety risks associated with handling powders and heat.
Comparing Powder Coating to Other Finishing Techniques
Understanding how powder coating stacks up against other finishing options is important for making informed decisions. Below are key comparisons.
Powder Coating vs. Liquid Paint: A Detailed Comparison
When comparing powder coating to liquid paint, several elements distinguish the two:
- Durability: Powder coating typically surpasses liquid paint in durability; it resists impacts, scratches, and degradation from UV light far more effectively.
- Finish Quality: The finish from powder coating is generally smoother and uniform, while liquid paint may show brush strokes or runs if not applied carefully.
- Environmental Impact: Powder coating is more eco-friendly. The lack of solvents in powder applications minimizes VOC emissions compared to traditional paint.
Performance Metrics: Durability and Resistance
When it comes to performance, powder coating often leads in key metrics:
- Corrosion Resistance: Powder-coated surfaces resist environmental stressors better than liquid paint, which can chip and corrode over time.
- Color Retention: Powder coatings often maintain color faster and longer, resisting fading due to UV exposure better than liquid counterparts.
- Heat Resistance: Certain powder coatings can withstand high temperatures without degrading, making them suitable for automotive and industrial applications.
Environmental Impact of Powder Coating
As industries move towards sustainability, the green credentials of powder coating come into play:
- Powder coatings reduce emissions due to the absence of solvents.
- Waste reduction is heightened through the ability to reclaim unused powder.
- Many powder formulations are non-toxic and environmentally safe, aligning with modern regulatory goals.
Expert Tips for Successful Powder Coating
When venturing into powder coating, whether professionally or as a DIY project, understanding the nuances can make a significant difference in results.
Common Mistakes to Avoid in Powder Coating
To achieve flawless powder-coated finishes, avoid the following common pitfalls:
- Poor Surface Preparation: Skipping proper cleaning and preparation can lead to adhesion failures.
- Inconsistent Application: Ensure that the powder is applied evenly to avoid thick spots or bare patches.
- Neglecting Safety Precautions: Always use recommended safety gear when handling powders and operating curing ovens.
Maintaining Powder Coated Surfaces
The longevity of powder-coated surfaces greatly depends on maintenance. Here are essential tips:
- Regularly clean surfaces to prevent build-up of dirt and grime, which can degrade the finish.
- Avoid abrasive cleaners that can scratch the surface.
- Check for and promptly address any signs of chipping or wear to extend the life of the coating.
Advanced Techniques for Custom Effects in Powder Coating
To stand out, consider advanced techniques that create unique finishes:
- Layering: Apply multiple coats with different powders to achieve textured or eye-catching effects.
- Custom Color Mixing: Blend powders to achieve specialized hues, though this requires ensuring compatibility.
- Specialty Techniques: Employ techniques like marbling or metallic finishes to create visually striking surfaces.